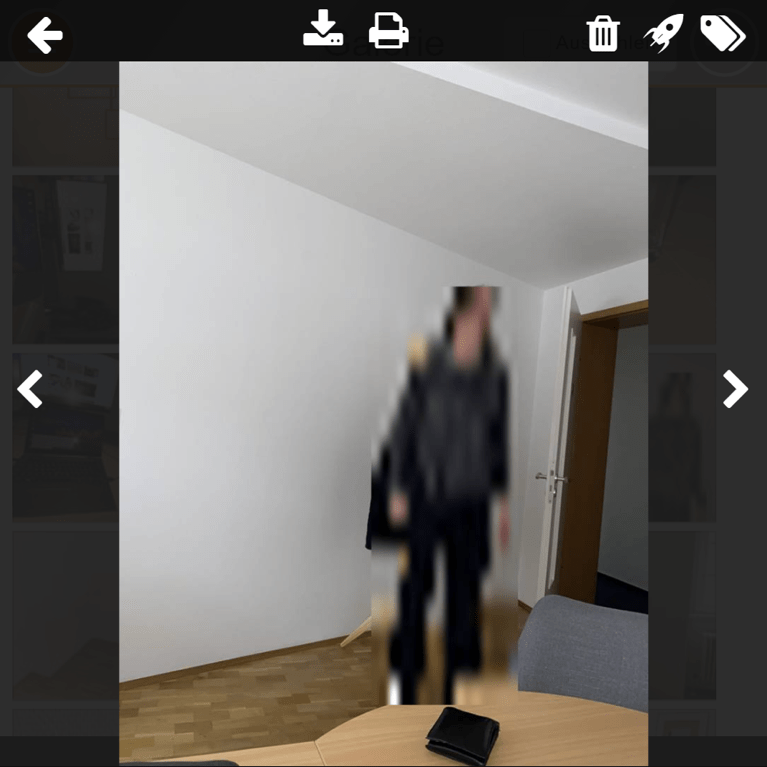
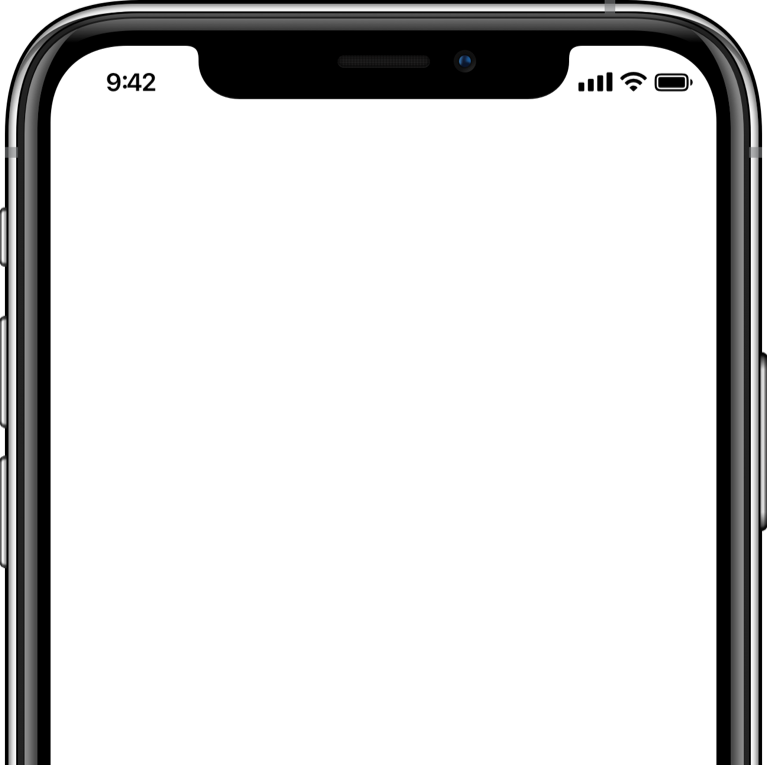
Recognition of persons or faces
- The service construction-photos
- object detection from images
- two modes: person or face detection
- pixelation of personal data
- DSVGO compliant image documentation
Artificial Intelligence is seen as the key technology for the future for the construction industry as well as for many other industries. Open Experience is positioning itself as a pioneer in this field.
Artificial Intelligence is seen as the key technology for the future for the construction industry as well as for many other industries. Open Experience is positioning itself as a pioneer in this field.
The goal of the ESKIMO project is to apply artificial intelligence (AI) methods to realize a much more efficient construction management. Three sub-goals are pursued here:
Image data captured during execution from smartphones, tablets, helmet camera systems, etc. are interpreted by AI algorithms. Building objects and their features are to be recognized in an automated way. Visual defects such as scratches or cracks can thus be directly detected and digitally processed.
The recognized building objects are compared with the topology of the BIM model, so that a virtual, continuously updated image of the current building condition including machines and materials is created. Based on this, it will be possible to identify performance progress and potential anomalies. This will dramatically increase the degree of automation of technical and commercial construction monitoring.
Building on image-based object recognition and topological matching with BIM, real-time position determination on the construction site will be developed using AI methods and sensor data fusion, which will be incorporated into intelligent systems to optimize construction processes. In this way, modern collaborative construction methods such as networked construction sites, just-in-time delivery, intel-igent construction logistics, clocked work methods, and lean construction will find practical application. This requires that data on the current and planned status is digitally available at the latest level.
The technical quality assurance module detects visual deviations from the target condition, i.e. surface features such as damage, stains, discoloration, etc., on the one hand, and structural differences from the BIM model, such as missing or incorrectly installed building elements, on the other, and records these defects automatically.
Commercial quality assurance takes on the challenge of determining a performance comparison based on the BIM model and reality. Regular actual recordings can be used to determine the time of installation of the individual construction elements and compare them with the planning based on the model.
Intelligent construction logistics focuses on logistical processes inside and outside the construction site so that the available resources, such as possible storage locations and process routes, can be used as optimally as possible.
The project "digiBau" aims at developing a modular and adaptable hard-software-system, which enables an automatic acquisition of digital information in the building industry. Through a module-based structure, this system should be able to be used on different "carrier systems". The envisaged technical solution is to consist conceptually and technically of the following software and hardware components, each of which fulfills a specific task and is to be developed independently of the others.
The sensor module consists of a mechanically flexible construction for holding various sensors, the attachment of which is made on the construction helmets. By means of an integrated software component, data from a wide variety of sensors is read in via a generic interface and made available for further evaluation by the digiBau system unit.
The camera module is a mechanically flexible component that is attached to a construction helmet depending on the examination procedure and at the same time contains a software interface for importing various image and video data that are made available for further evaluations in the analysis module of the system unit.
The system unit employs hardware and software innovations to enable sensor data processing, image processing, navigation and defect analysis. It essentially consists of a database within which the sensor, image and video data are combined in an analysis module. By means of special algorithms, the image/video data of the examined object (room, building facade, plant, etc.) are merged there together with the acquired sensor data in real time, which requires a powerful computing unit. This then produces a realistic overall picture of the object under inspection with concrete data on the various object dimensions and inspection measurements.
The Smart Inspection Cockpit is a mobile application for field staff that enables real-time communication between the system unit and a mobile end device (smartphone or tablet). Here, the employee carrying out the inspection is shown the image and sensor data compiled in the system unit graphically and the defects identified via the analysis module of the system unit (cf. M3) are visualized directly with the respective position information. Thus, if necessary, even further investigations can be carried out on identified defects, which are triggered directly from the cockpit, e.g. zooming in on a construction defect via the camera of the construction helmet for photo documentation and simultaneous addition of digital annotations / texts / voice notes.
The backbone of the system is the inspection server. This accompanies all inspection and analysis processes and provides data management functionalities as well as further analysis algorithms for offline processing of the data. For example, historical data will be compared to new data from the current object inspection to identify dependencies and anomalies using computer learning algorithms. Examples include the recognition of patterns and dependencies on defects that have occurred with respect to materials, usage behavior, or interactions with the environment. The information gained from this is to be made available as (optimization) knowledge for future construction projects, which is why a further step is the internal processing of the information via the inspection server.
Open Experience is responsible for implementing the software modules in the project.